Cranedge Resonates Shop-Floor Safety
Workplace safety is of utmost importance for any assembly unit. Every company tries to eliminate hazards by implementing HSE policies that safeguard the workers & operators on the shop floor. However, the employees must also take care of their safety and adhere to the safety rules laid down by the company. Generally, all industries design their safety guidelines in order to minimize the risk of injury to the stakeholders, may it be customers for a factory visit, workers, operators, or staff members. What they miss is the regular servicing and checking of the equipment they work with. Accidents that might take place on a shop floor, could be due to improper usage of equipment or due to low maintenance of equipment.
However, sometimes it also happens that in spite of good maintenance, certain equipment with old or obsolete technology, tends to pose a great threat to the safety of the shop floor. Such equipment not only requires good health check-ups but also requires upgrading to newer parts and upkeep with additional enhancers to make work with other modern requirements. Below is one such incident, which explains why safety should be a priority on the shop floor:
Case Study
One of the largest vehicle manufacturers in India well-known for its range of passenger vehicles and tractors faced a security threat in one of its manufacturing facilities near Pune. The plant oversees the manufacturing of heavy parts required in the vehicles and operates in 3 shifts. This plant, being set up in the initial years of the company’s operations still continues to use older machinery and equipment for its material handling needs.
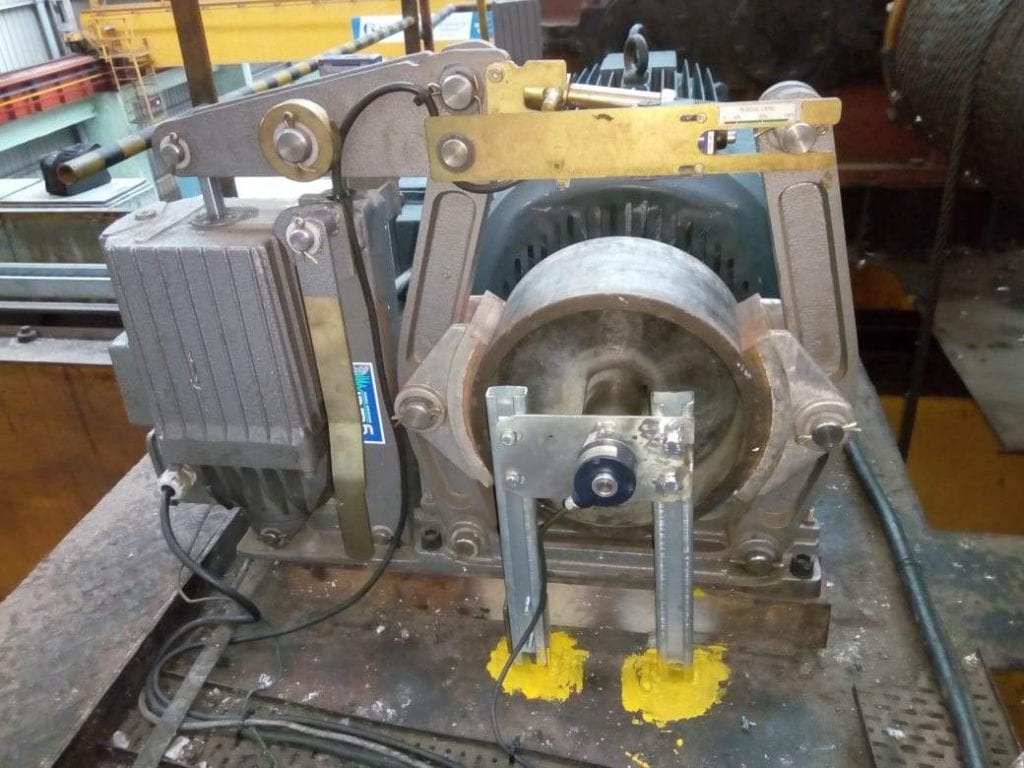
One day, during routine operations, a heavy load was being handled using one of their older cranes when suddenly, the load slipped off and fell from a height of 5.5 meters. Fortunately, there were no casualties, but serious damage was caused to the machinery & the floor, which resulted in financial and operational losses. The incident sent immediate ripples within the plant, and the issue was informed to plant heads of different units to take due diligence.
This also shook the corporate office as the crane posed a real threat to the shop-floor safety. It was high time for a company which is known for its adherence to the highest level of safety standards to take the incident very seriously. A thorough probe was initiated, and an immediate “why why” analysis was done to find the causes of this mishap, and it was decided to consult industry experts. That’s when Cranedge was called in to investigate the accident, suggest as well as implement a foolproof solution as well as undertake health check-ups for other cranes, not only for the Pune plant but also for other plants across India.
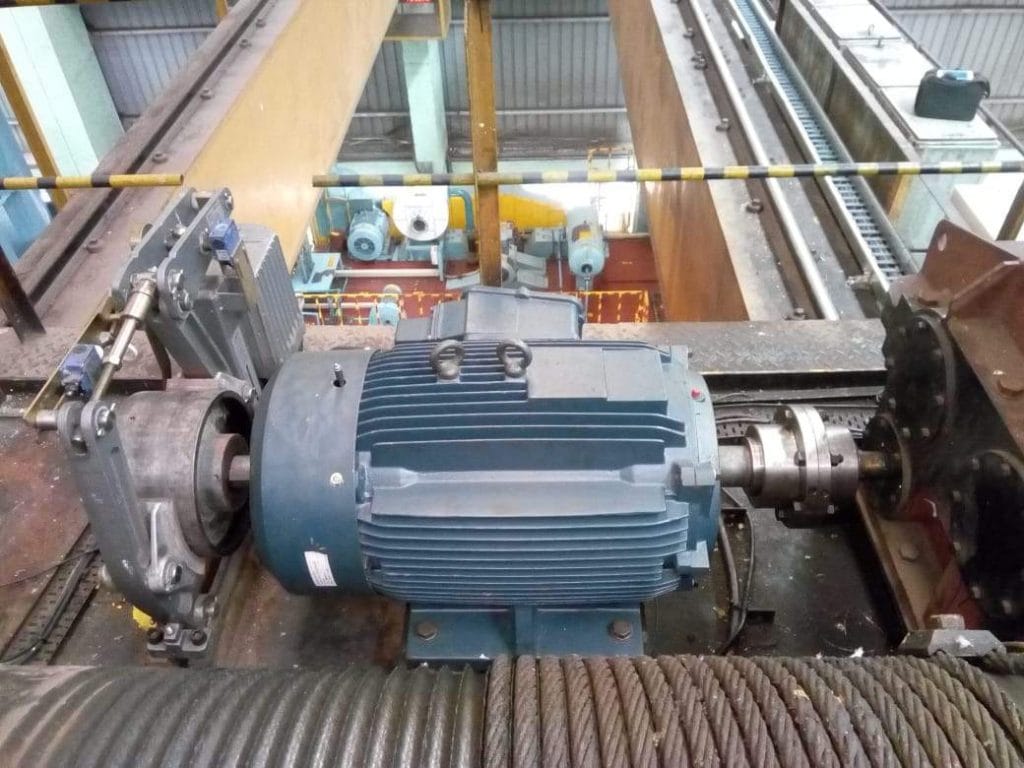
Our Solution
The Cranedge team of specialists visited the plant to investigate the cause of the incident. Their preliminary investigation revealed that it was due to the failure of the hoisting brake and that it had no contingency measures. Just to be on the safer side, our team conducted a thorough Health Check-up of the entire crane with structural analysis (FEA) of the main girders and another visual & functional diagnosis.
A complete report on the present condition of every major component of the crane was submitted to the customer along with our recommendations for additional features to ensure higher levels of safety. The additional features included:
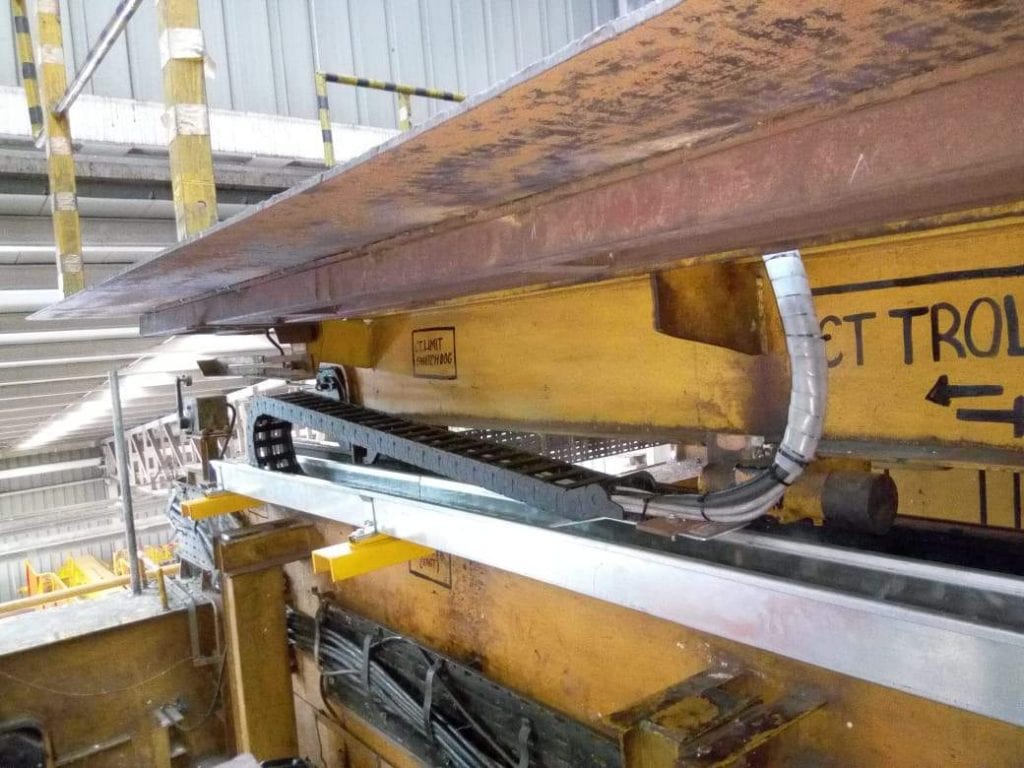
1. Variable Frequency Drive (VFD):
The existing crane being used of older technology; it had slip ring motors on existing hoisting machinery. Today, the industry has advanced, and the slip ring motor (being almost obsolete) has its own limitations as against the combination of a squirrel cage motor and a VFD that offers better control. VFD being more energy-efficient also helps in reducing energy consumption. Considering these aspects, Cranedge modified the hoisting machinery by replacing the slip ring motors with a new squirrel cage motor and VFD’s in electrical circuits.
2. Anti-fall System:
In case the main brake fails, the crane’s electrical system will immediately trigger as it will detect load-free fall and deploy counter measures. Here, the motor will give a reverse torque to uphold the load for a few mins with the assistance of the VFD. The system also automatically triggers a siren warning to the operator and the people in the vicinity are well informed about the emergency situation. Furthermore, it was suggested to the client that for certain select, critical application cranes, an “emergency brake” could also be deployed. This critical time interval allows the operator to safely lower and park the load at a safe location.
New Control Panel and Drag Chains :
The crane was upgraded with completely new electrical panel housing and VFD’s along with encoders and other circuitry controls along with a new robust drag chain system.
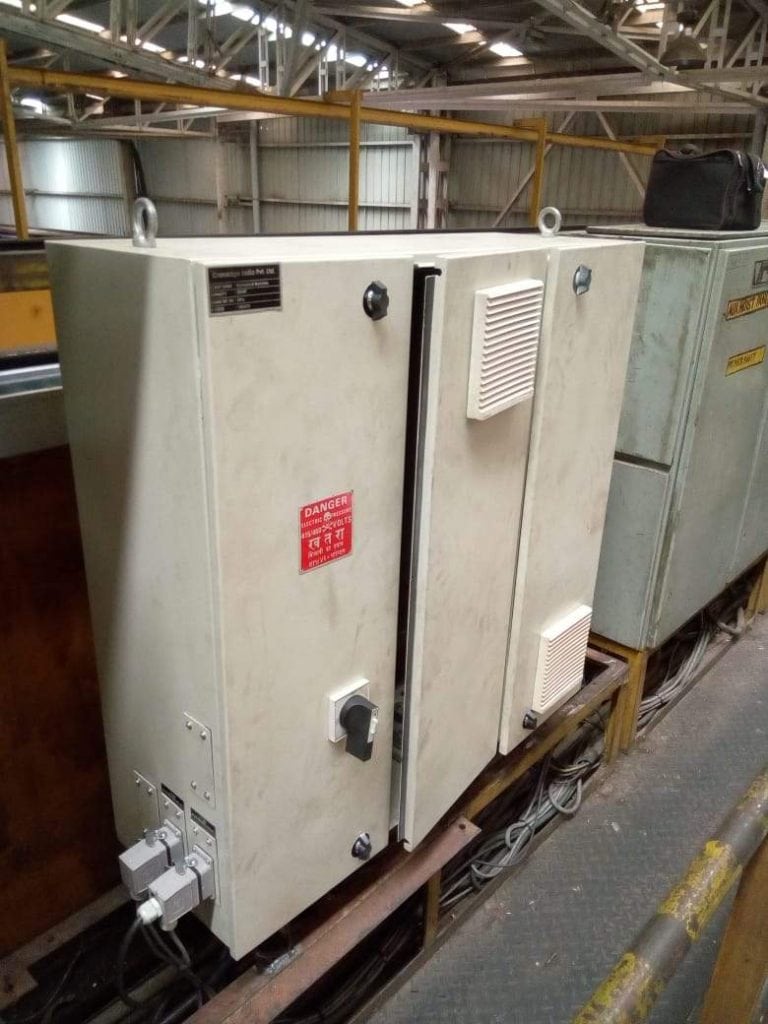
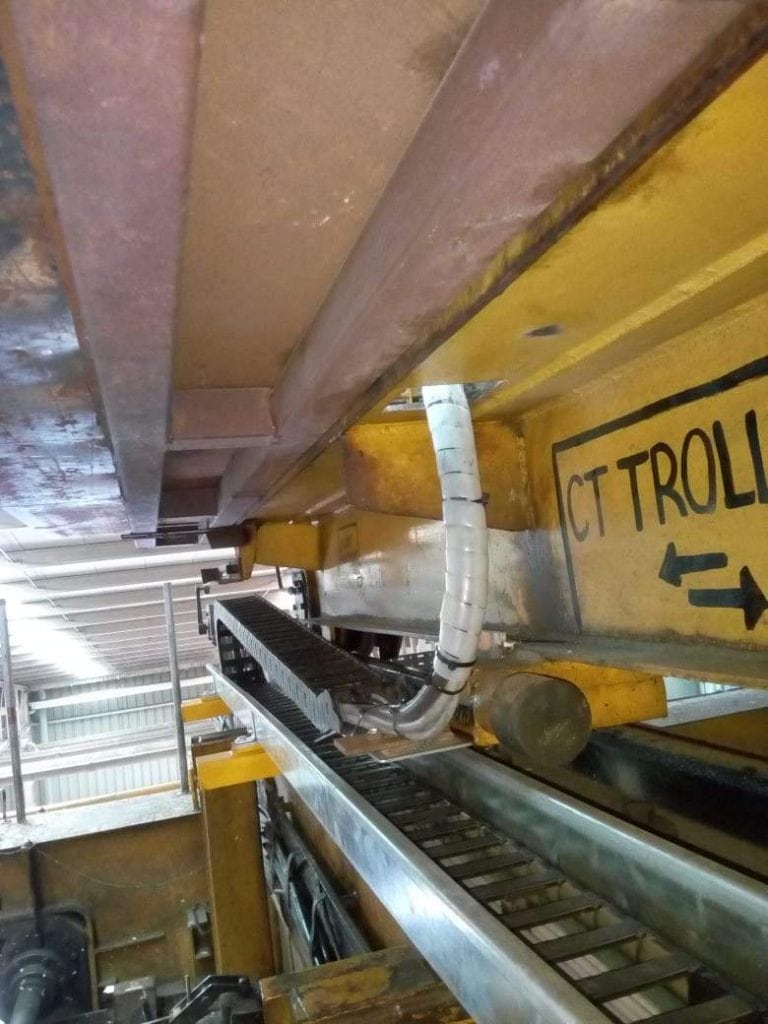
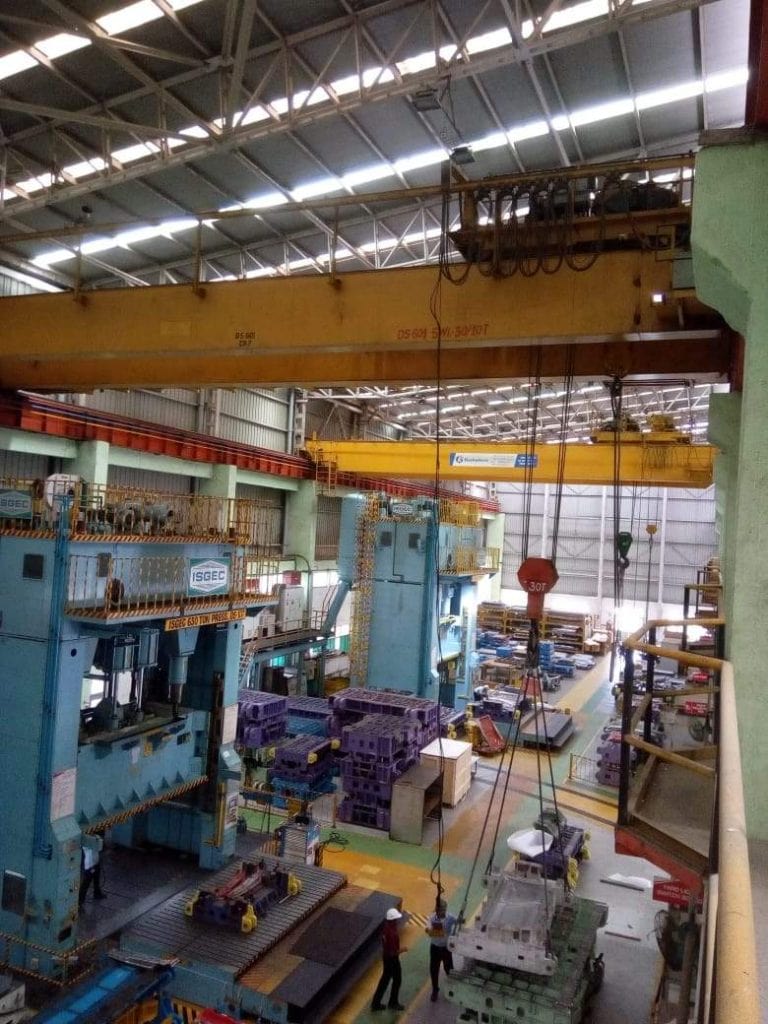
Thus, Cranedge provided a quick diagnosis of the problem and a viable techno-commercial solution to the manufacturing plant and instilled a sense of assurance within the stakeholders about the safe operation of the crane in the future. For more such servicing solutions for your cranes, visit https://www.cranedge.com/