Safety Starts with our Crane AntiFall System
What are Falling Materials and Why are they a Cause of Worry? – A Case Study
Falling materials are a major concern at any workplace or plant site wherever overhead cranes are installed. Load slippage, mechanical failure, or operator incompetency can all result in serious injuries or fatalities. If loads are not properly secured, the load can slip and land on workers in the vicinity or cause major damage to property. Loads being lifted by overhead hoists tend to be fairly heavy and cause serious damage when they eventually crash to the floor.
One of our prestigious customers and a major Indian auto giant faced one such unfortunate incident wherein the load from a 25t DGEOT crane, slipped and fell from a height of 8 meters. Although there were no casualties, there was some serious damage done to the machinery and there was the loss of property. This incident shook many within the company and posed a real threat to safety at the workplace. The customer is one of the most reputed companies that gives the utmost importance to the safety of its employees, immediately decided to consult one of the best in the business. Cranedge India Pvt. Ltd. with a decade of experience in EOT crane services, was invited for a detailed discussion to understand the reason for the mishap and to come up with an optimal solution to avoid any future accidents.
Crane Specialists at Work!
Cranedge sent a team of crane specialists, who went about their job with an eye for detail. They thoroughly checked the crane, analyzed the site & the application and even interacted with the crane operator and the workers to detect the reason for the failure. Backed by a strong design team, Cranedge came up with a bespoke solution with minimal changes in the existing system. The customer was so impressed with the technical expertise and the approach of the Cranedge team that they decided to place the order for executing the solution on not just one but 10 of their critical cranes at the same time.
Since the cranes were more than a decade old, Cranedge team conducted a thorough check on the cranes to understand the condition of the crane. The crane data were further analyzed with the Design team in consultation with the sales and service team to understand the requirement of the customer and to device a system that was both cost-effective as well as ensured a safe working environment with minimal changes in the existing system.
Our Solution
Crane Anti-Fall system was designed as a safety measure to alert the operator and the workers during the time of emergency. In cases where the hoisting brake fails, an alarm would go off notifying the operator and the workforce about the emergency. At this stage, the system is capable of holding the load for a period of around 10 minutes even after the hoisting brake completely fails thereby allowing the operator sufficient time to park the load at a safe location without having to worry about the load falling down. Once the situation is taken care off, the crane can be maintained and made ready for use once again.
The MH slip ring motors were replaced with VFD suitable squirrel cage motors, New VFD control panels with other accessories were provided, cable trailing systems were replaced with more robust drag chain systems. This system was implemented one by one, on each crane and was made ready for operation in a week’s time.
Though the Anti-fall system proved to be a real boon to enhance the safety of the crane, performing regular maintenance can be one of the easiest ways to reduce the risk of falling materials. Maintenance should always be of paramount importance when it comes to heavy machinery. If a moving part on an overhead crane wears out or breaks the hoist, it can cause serious damage. Performing regular maintenance ensures trouble-free and smooth operation of the hoists and overhead cranes. Cranedge India Pvt. Ltd offers a wide range of crane services that are customized according to the requirement and application of the crane. To avoid human error, Cranedge has also strategically developed advanced equipment’s like RAMON (Rail Monitoring System) for precise inspection & correction of crane geometry & rail alignment and ROMON (Rope Monitoring System) for timely prediction of rope failure.
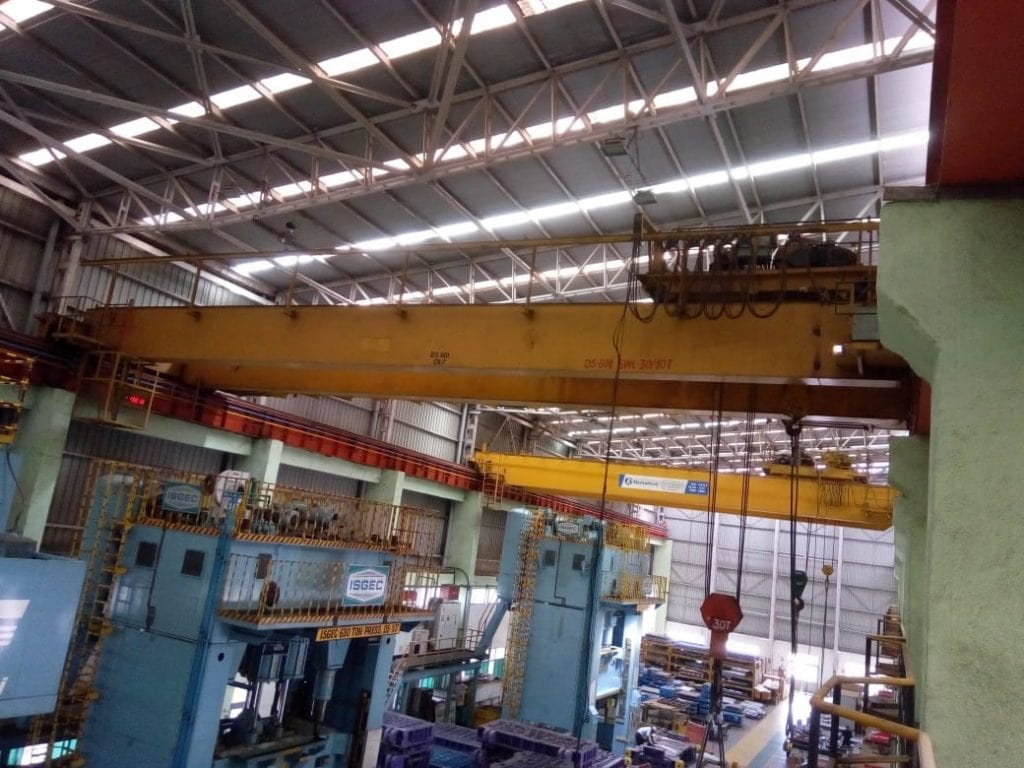
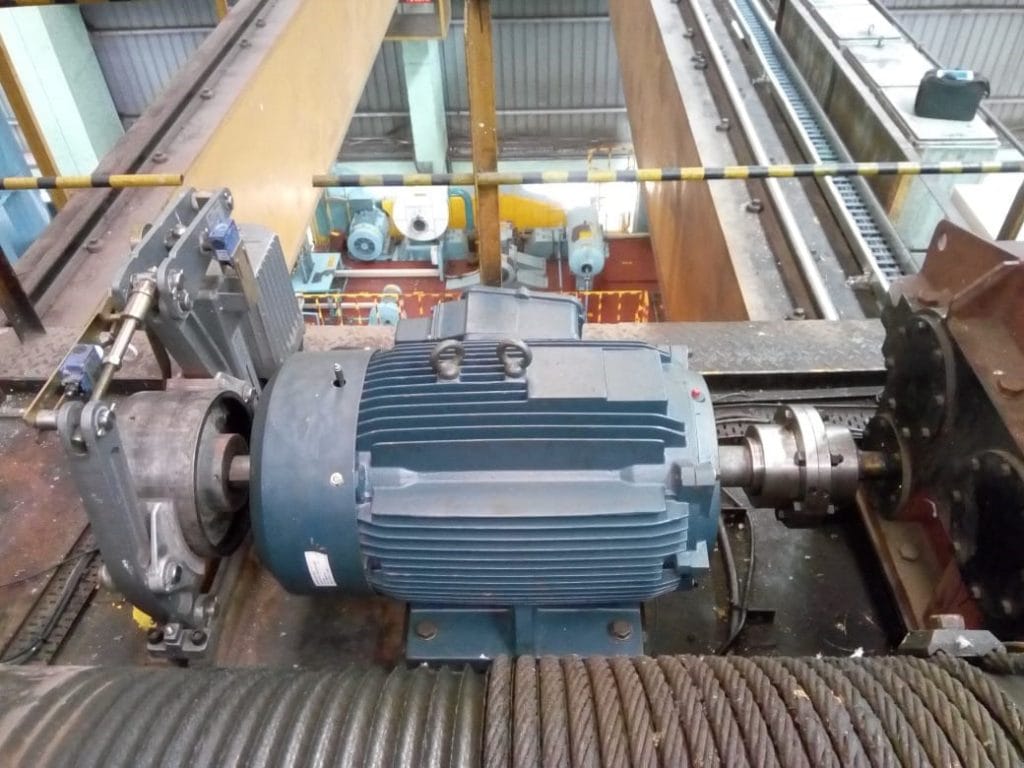

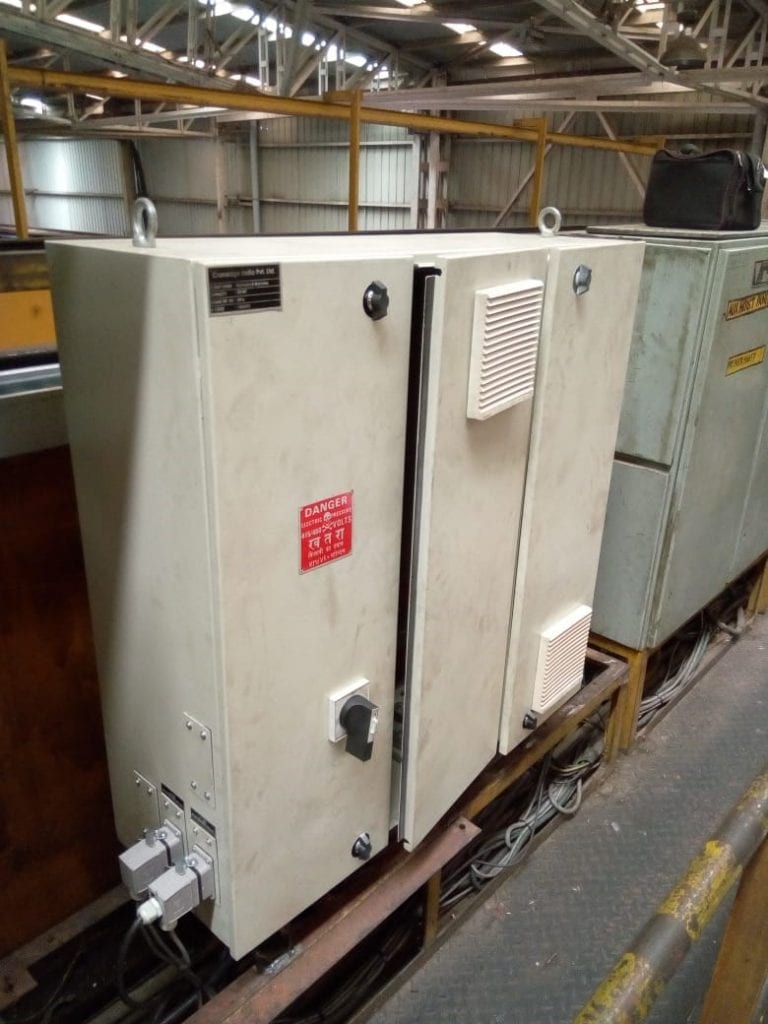
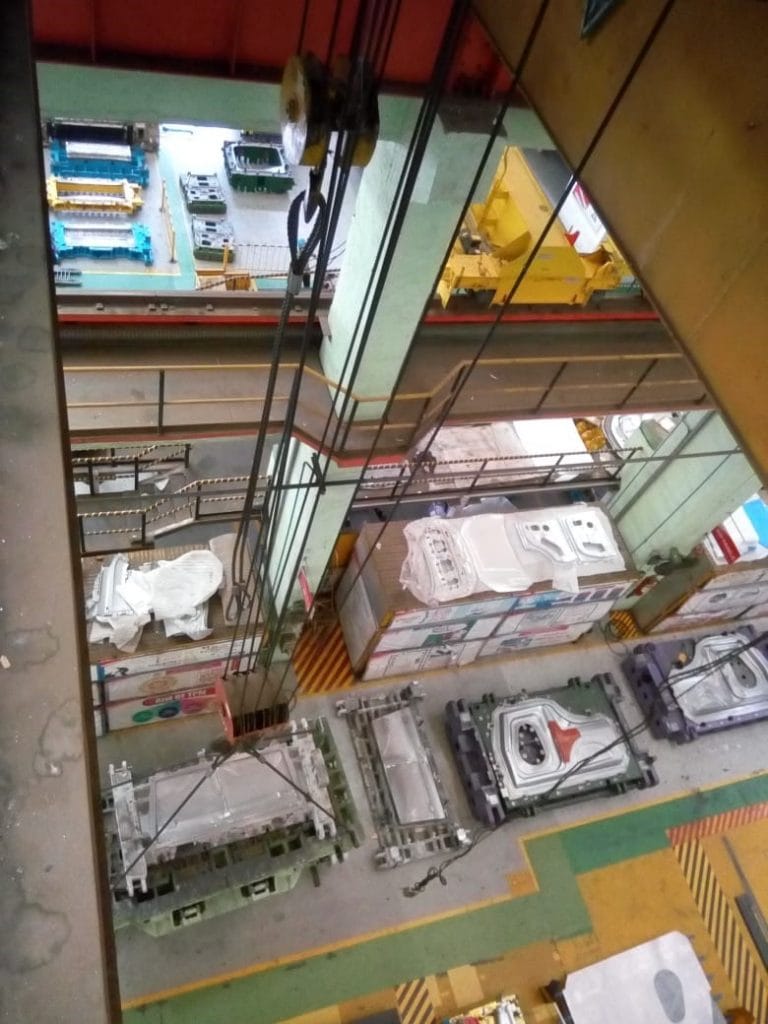
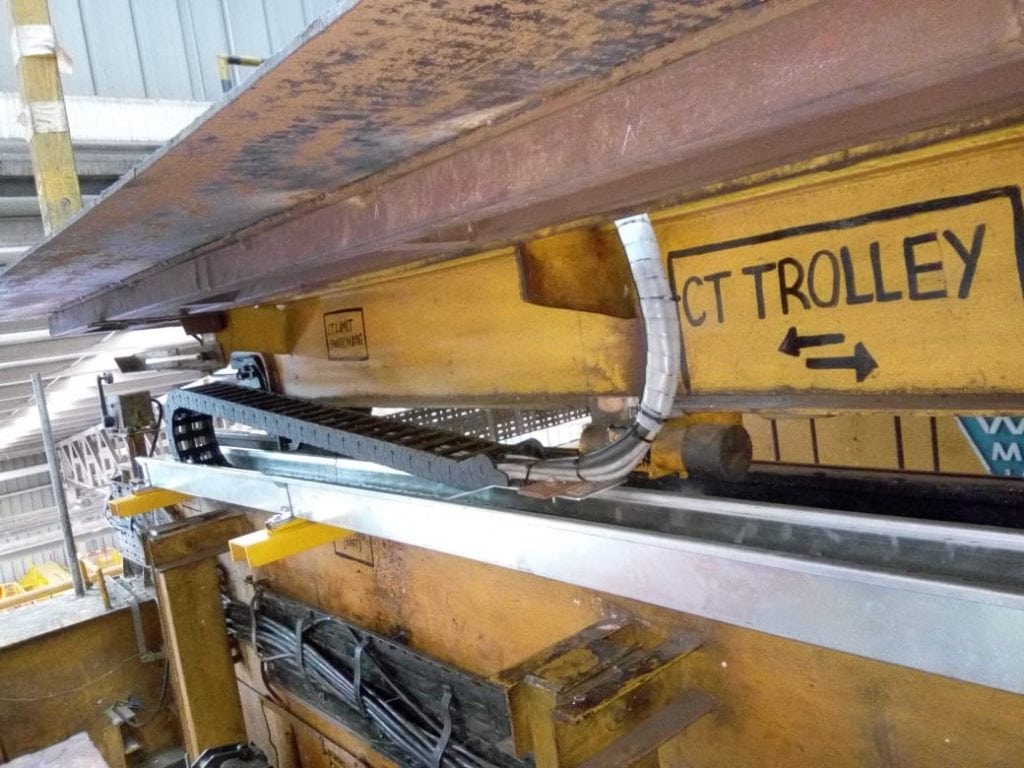